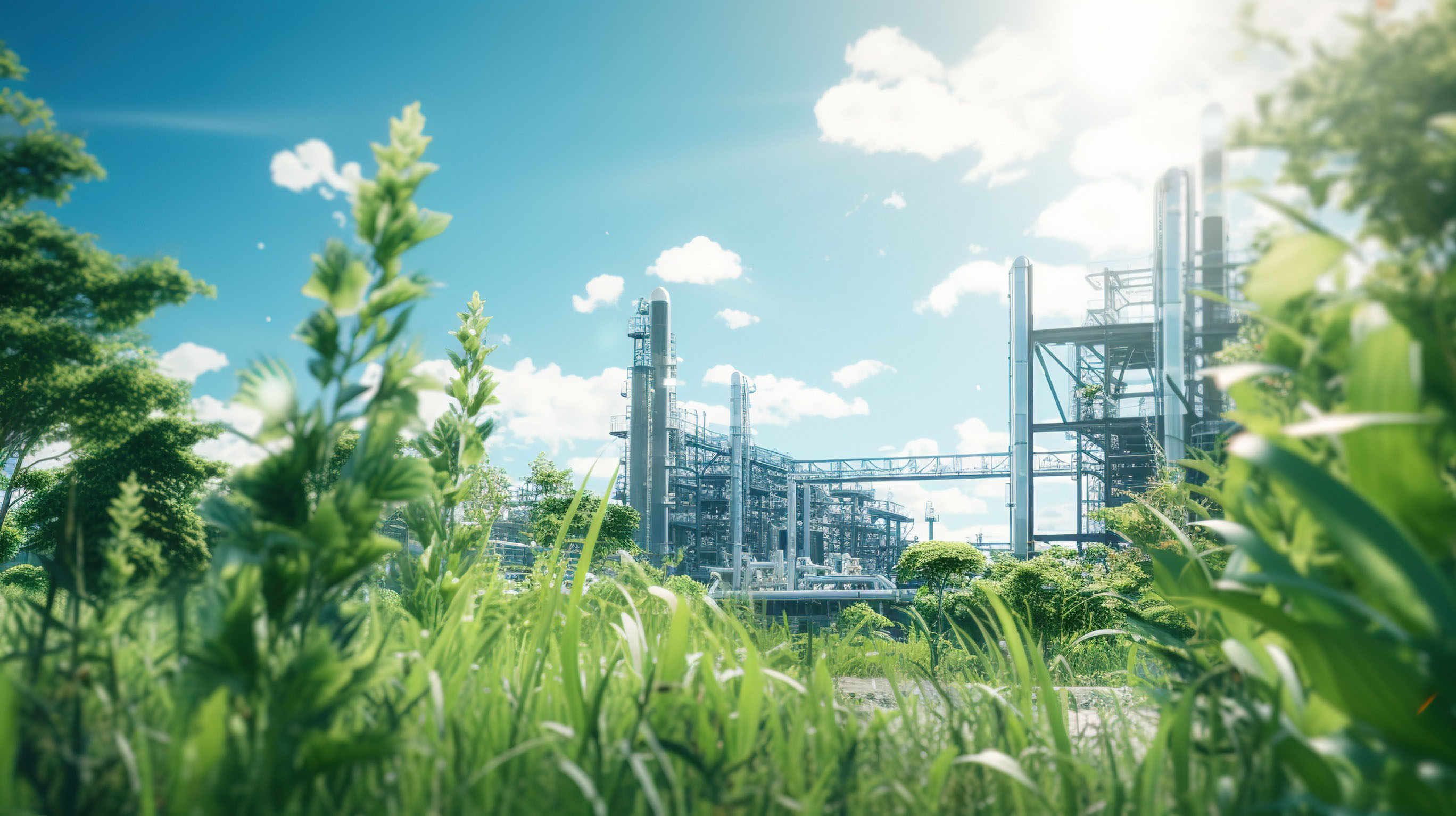
Ecology in plant engineering
From the producer's point of view, aging resistance, resistance to the penetration of moisture or measures to avoid diffusion are the first steps towards active environmental protection. Materials that are characterized by lower emissions and minimized use of raw materials during production also support the trend towards ecology in industrial plants. Special features of pre-insulated pipes from the RAPID and FIRESAFE® product series: They are crush-resistant and rot-resistant. Material that is not subject to aging does not require replacement, repair or maintenance. During installation, sleeve connections, branches and bends are insulated with the same material. This guarantees consistent operating conditions for the pipe system and safe processes.
Reduction of energy use
The reduction in energy use, durability and system safety set the company's benchmark for the development of an alternative pipe concept for industry. Another aspect: reducing energy (CO2) and minimizing the use of raw materials. As the results of the investigations into marketable alternatives show, the material polyurethane (PU) proves to be the ideal solution for the pipe concept in two respects. The production of larger foam volumes requires only small amounts of raw material with an expansion factor of up to 1:20 and a minimum of energy. Reacted foam is also environmentally neutral and can be disposed of as municipal waste.
Minimizing the use of raw materials
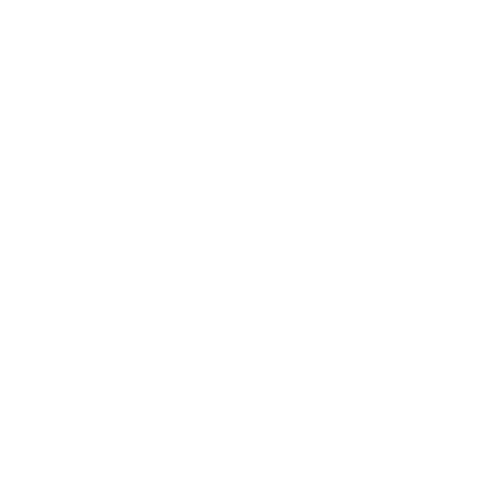
The reduction in energy use, durability and system safety set the company's benchmark for the development of an alternative pipe concept for industry. Another aspect: reducing energy (CO2) and minimizing the use of raw materials.
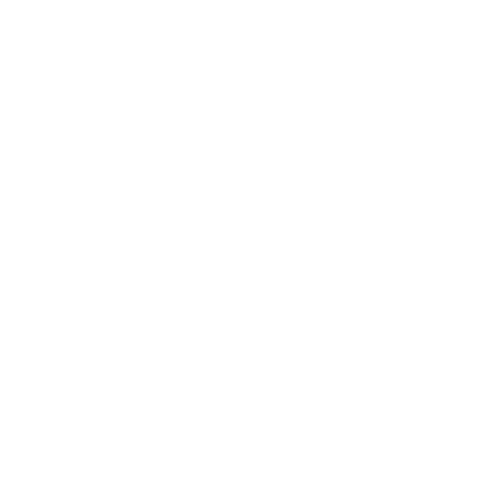
As the results of the investigations into marketable alternatives show, the material polyurethane (PU) proves to be the ideal solution for the pipe concept in two respects. The production of larger foam volumes requires only small amounts of raw material with an expansion factor of up to 1:20 and a minimum of energy. Reacted foam is also environmentally neutral and can be disposed of as municipal waste. Remains from on-site production/installation can be returned to the material cycle and used to produce recycled material or thermally utilized.
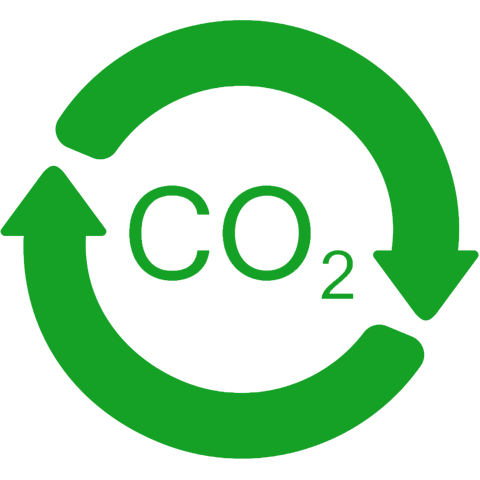
The simulation of the operation of a planned system based on different pipe concepts with a process temperature of +50°C showed significant energy savings with pre-insulated pipes. Specifically, 1,000 MWh of energy is saved annually and the environment is relieved of 200 t of CO2 annually.
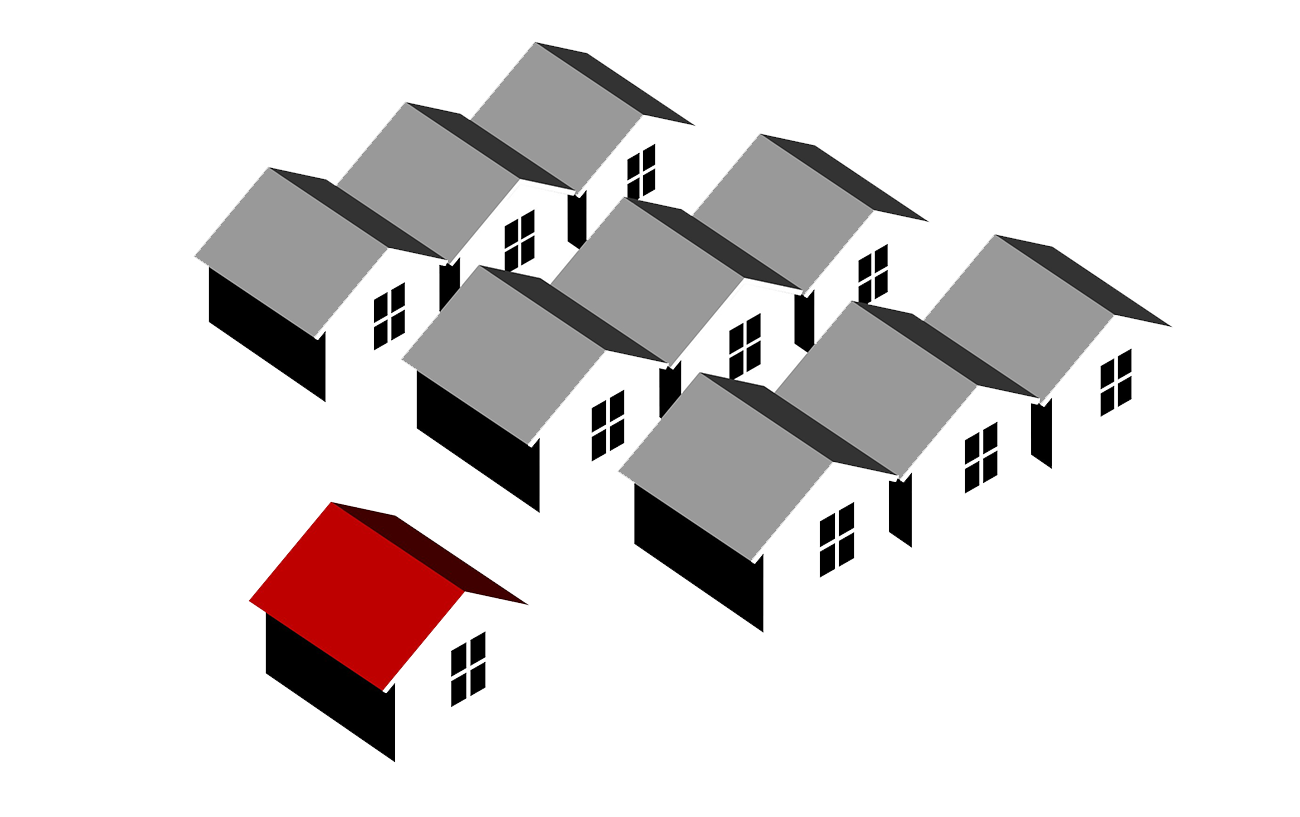
The energy consumption for heating and operating 100 single-family homes is practically saved. The use of the latest developments in plastic technology in the insulating foam for pre-insulated pipes ensures comprehensive fire protection and extended safety with certified FIRESAFE® T30, FIRESAFE® T60 and FIRESAFE® T90 classifications.